The aim of this paper is to demystify fuel additives (combustion improvers) in just 1500 words or 10 minutes of reading. It will cover, what they are, why they exist and how they function.
Unfortunately “Fuel additives” are often associated with horror stories and skepticism. So, let’s begin and see how I can address that elephant in the room.
Combustion Improving Additives – The objective is to improve fuel performance by maximising the total energy potential of the fuel at combustion.
One misconception to be addressed right from the start is the misgiving that fuel additives improve engine performance. I understand why this statement is made however I challenge this statement and suggest fuel additives improve fuel performance.
The point I make here is that there is rarely anything wrong with engine designs these days and they don’t necessarily require improving. It is the fuel that most often requires improving (actually I mean repairing but I’ll explain later) to perform as it was intended/designed to, and this improvement in fuel performance has the knock-on effect of the engine performance improving, however the engine is only performing as it was design to.
This may seem like I’m splitting hairs however the focus needs to be on the fuel, not necessarily the engine.
Why do we strive to improve combustion?
A complete combustion = all fuel burnt = fuel efficiency
A complete combustion = no residual carbon/soot = lube and components optimisation
A complete combustion = less harmful emissions = smaller carbon footprint
There are two methods to achieve this, you can either:
1.) Enhance Combustion – By amplifying the fuel
2.) Improve Combustion – By conditioning the fuel
Additives to Enhance Combustion- These are solvent based, they change cetane, they lower flash points or oxygenate fuel. These are volatile products and require dosage controls. They change fuel chemical specifications and deliver a bigger bang.
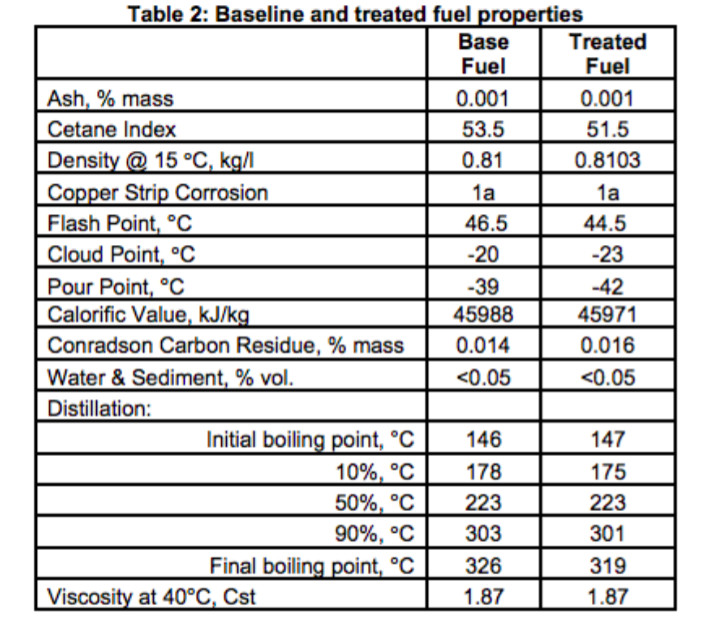
Above is a table showing how fuel specs can change when using this fuel solvent additive. In this case the flashpoint is lowered from 46.5 C˚ to 44.5 C˚.
Solvents based additives can contain ethanol, naphtha, kerosene and other lighter petroleum products which lower flash points for an earlier ignition and longer burn as well as nitrates and peroxides to increase cetane numbers for a more rapid ignition.
Solvent based additives with flash points close to the fuel are dose sensitive and should only be handled by fuel producers when blending to meet fuel standards.
All of the western world have strict fuel standards, with minimum and maximums and there should not be a requirement for suppliers and users to raise cetane levels or change flash points.
Additives to Improve Combustion – These are non-solvent detergents, they disperse molecular agglomeration in fuel to restore the fuel’s physical composition. These are nonvolatile products without dosage risks. They do not change fuel chemical specifications and deliver a complete bang, but not a bigger bang.
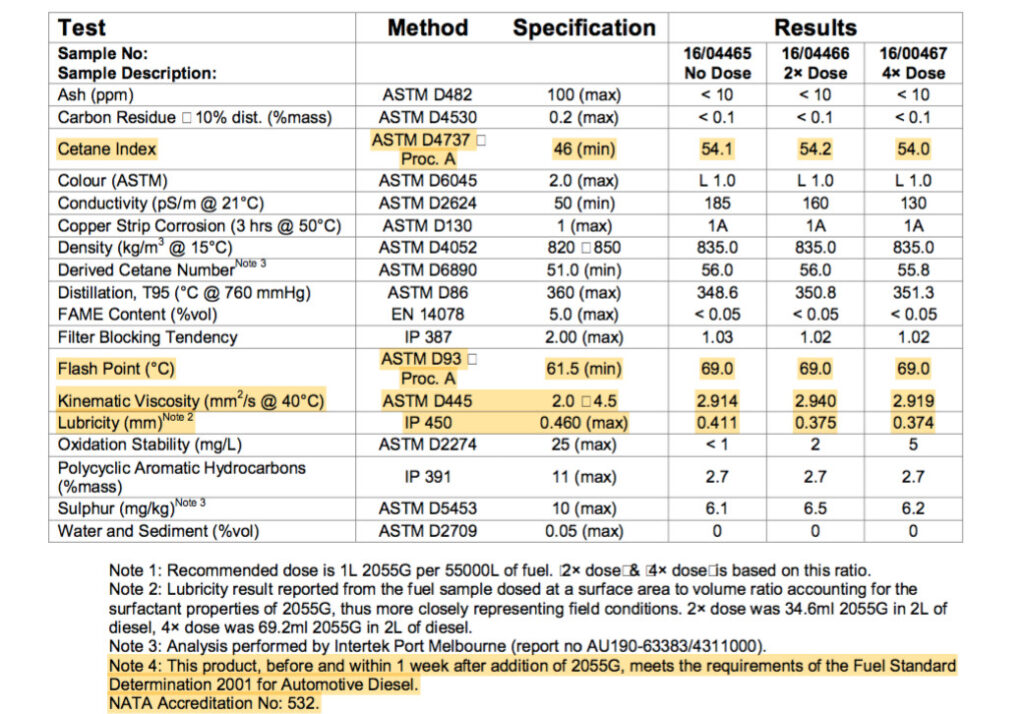
Above is a table showing how fuel specs are not changed when using a PURE fuel detergent surfactant additive. Cetane and Flash Points remain the same. However, the Lubricity value is improved.
How do you know which is which? – Generally, an additive’s Flash Point is an indicator.
Additives with Flash Points south of 80˚C usually indicate solvent based inclusions
Additives with Flash Points north of 120˚C usually indicate non-solvent based – this is why these can be used in all fuels, from lighter gasolines, diesel distillates right through to heavy fuels without risks.
Logically the closer the additive’s Flash Point is to a fuels Flash Point the more likely it can alter the ignition timing, combustion length, and size. The higher and further away from the Flash Point to the fuels the less likely it can have any impact.
Solvent-based additives are catalysts that can affect ignition timing. They enhance (amplify) the combustion’s size and length.
Non-solvent detergent based additives only have a physical effect. They condition the fuel to perform at its best.
Another misconception to address is the myth that detergent additives clean engines. The word detergent is misleading and makes us think of cleaning agents. It is through the constant recurring of a complete combustion that engines become clean of carbon fouled injectors, carbon in chambers and soot in lube. They will only remain clean if the combustion remains complete. The opposite is true; dirty engines are simply engines with a recurring incomplete combustion.
So, why are additives important today?
We need to go back to the start and look at the crude barrel of oil to identify why fuel loses its efficacy more rapidly and today requires additional help to perform.
Let’s start with how fuel refining has evolved.
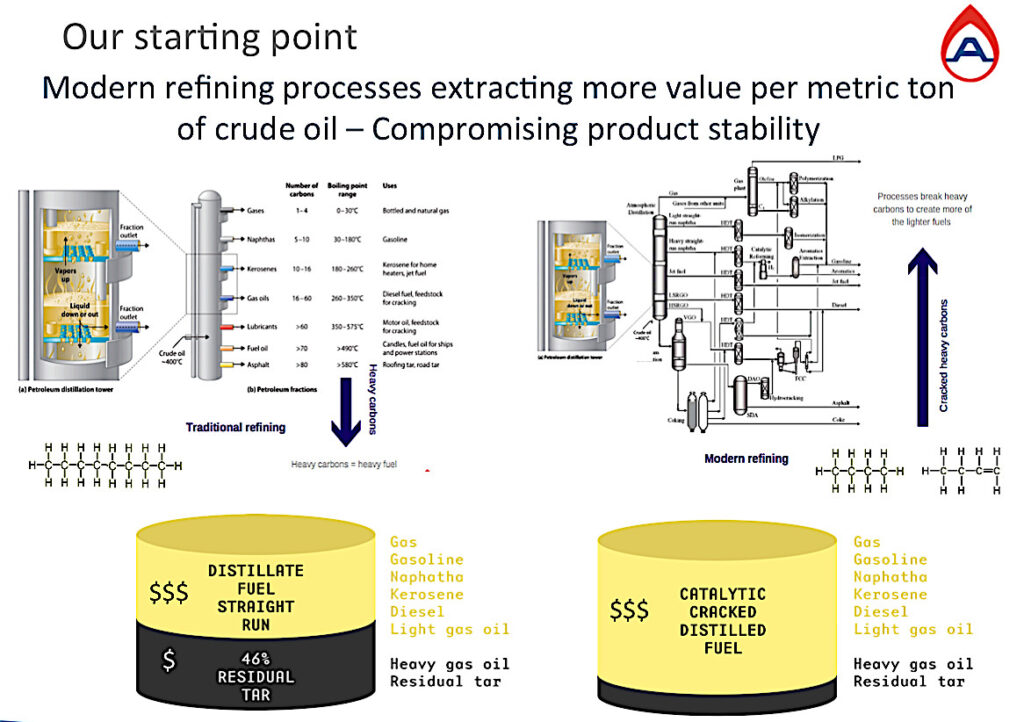
This slide above shows the evolution of refining over circa 15-40 years depending on the refinery and region. Traditional refining on the left and modern refining on the right.
In traditional refining the hydrocarbon chains are heated to between 350˚C – 400˚C to separate the hydrocarbon chains by size and then they find their weight and place in the column.
The heaviest chains with many carbon atoms would account for almost 50% of the oil barrel remaining as residual tar generally used to make roads and without much value, whilst the lighter chains became our gas oil, diesel, jet fuels, gasoline, and gas. Increasing in considerable value the lighter they get.
So, the gas and oil industry’s aim is to produce as much of light fuels as possible from an oil barrel, to achieve the highest value per barrel of oil.
The modern refining solutions came with complex fractioning and cracking methods resulting in the barrel of oil-producing mostly lighter fuels with less than 10% remaining as residual tar.
The length of a hydrocarbon chain depicts the weight and type of fuel. The fewer carbons, the lighter and more valuable. The aim is to fraction or crack the hydrocarbon chains into smaller and smaller chains.
The molecular impact on modern refined fuel
In traditional refining, many chains are like the figure below, ranging in a different number of carbons. In this example, the hydrocarbon chain has 8 carbons and 18 hydrogens atoms C8H18 this is an alkane hydrocarbon or also known as a saturated hydrocarbon where all the electron gates are locked and stable.
_______________________C8H18 Stable (saturated) Alkane________________________
In modern refining, the chain has been split (cracked), where half remains saturated C4H10 (left figure below) with all 4 electron gates of the carbon atoms used, but the other half becomes C4H8 hydrocarbon (right figure below). It is now missing two hydrogen atoms and is no longer a saturated hydrocarbon, but becomes an alkene or an unsaturated hydrocarbon with a double bond (c=c). These are the troublemakers and unstable ones.
_____________Stable (saturated) Alkane_________Unstable (un-saturated) Alkene______
Why are un-saturated (c=c) chains unstable?
Because each carbon atom has 4 electrons in blue below and each hydrogen has 1 electron in red, these are the magnetic connectors between atoms.
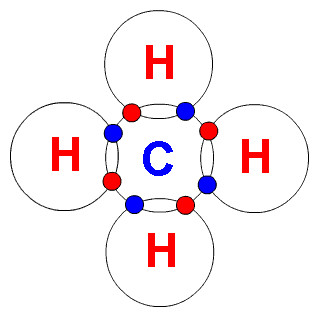
When we crack a saturated chain (fully connected) we end up with smaller (lighter) chains, but every half has a shortage of hydrogens and so they become un-saturated (alkenes) a double bond hydrocarbon (image above right).
The unsaturated hydrocarbons seek to bond with missing hydrogens or other atoms and this is where the problems start and agglomerations begin. The agglomerations start forming as soon as chains are cracked. Modern refining involves multiple cracking and fractioning to achieve the most value from the oil barrel.
Fuel stability has slowly been compromised, so slowly over many years that the change was barely noticeable and just became the new normality.
So much that still today engineers will more often question there operations and adapt to the fuel rather than question the fuel performance itself.
The escalation and new reality
In recent years blending of fuels has also been introduced, along with tighter EPA engine emission technology both have contributed to VW and other OEMs the need find creative methods to avoid Particulate Filter breakdowns.
Ultra Low Sulphur fuel is now in great demand and very costly to produce. One economical method that has been adopted is the commingling of fuels from different refineries and regions to reach a re-blend to deliver the required sulphur content and specifications demand of each market.
Please note; When fuels are refined in one refinery and from one region with strict re-hydrogenation controls, instabilities are less likely to occur. However, today these fuels are very costly and rarely available.
Another additional complication with sulphur is that sulphur is a natural preservative and without it a fuels tendency to oxidise is increased.
So now we have a mix of unstable chains co-mingling with other unstable chains from different refineries and regions, resulting in even more rapid agglomerations. Not even the best-engineered engines can manage a complete combustion.
To add one more spanner to the works – biofuel blends are also contributing to agglomerations as the majority of the hydrocarbons are naturally un-saturated double (c=c) bonded, alkenes.
The result is a fuel that requires higher pressure and higher heat to fully burn than the engine is designed to.
As a result carbon and soot builds up inside the chamber, injectors fault prematurely, lube oil TBN’s are compromised sooner, particulate filters cannot cope and operations require shorter maintenance schedules.
So how do detergent based additives resolve this?
The only additives that can reverse agglomerations are dispersants, what I refer at the beginning as a combustion improver, dispersants physically put the fuel back into its originally intended composition.
Water is H2O and the hydrogen is also attracted to the double bond (c=c), as discussed above and emulsifies with fuel. A concentrated dispersant surfactant also de-emulsifies 99.9% of water – separating water and protecting fuel from microbial growths (cfu’s) replacing the need for biocides.
Dispersant Sufactant in action:
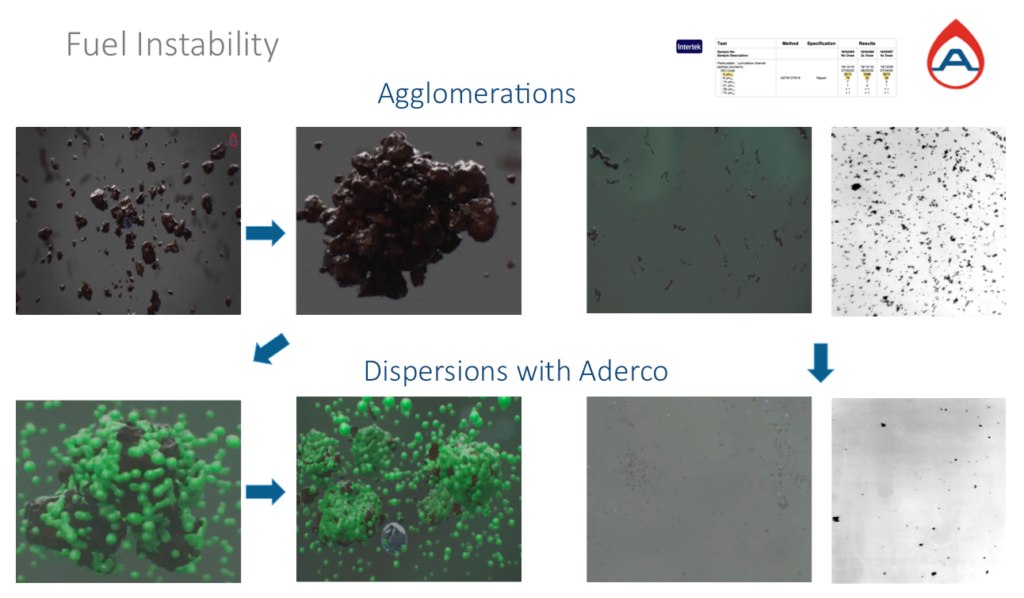
The top left images show the start in agglomerations of the un-stable hydrocarbons and below shows a dispersant molecules in green working by attaching themselves to all the hydrocarbon surfaces and splitting up any agglomerations and separating water. The molecule acts as a replacement for the shortage of hydrogens and stabilises the alkene (un-saturated) hydrocarbons inhibiting the possibility of further agglomerations.
Above far right images show the difference before and after through a microscope.
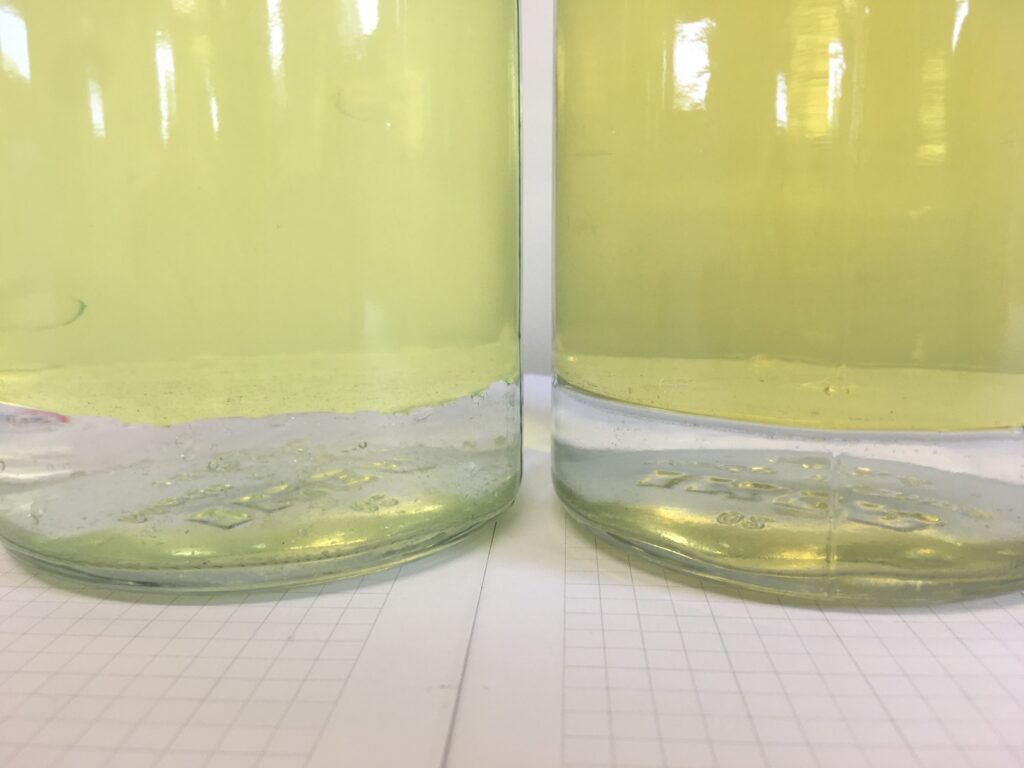
Left Image; We deliberately added water for this. Note the difference in the line of separation between fuel and water. The treated fuel on the right has a clear separation inhibiting microbial access to water and fuel. The untreated bottle on the left shows signs of emulsification between fuel and water, an environment where microbial life can be supported.
Below we have an ISO particle count also showing the same dispersant effect.
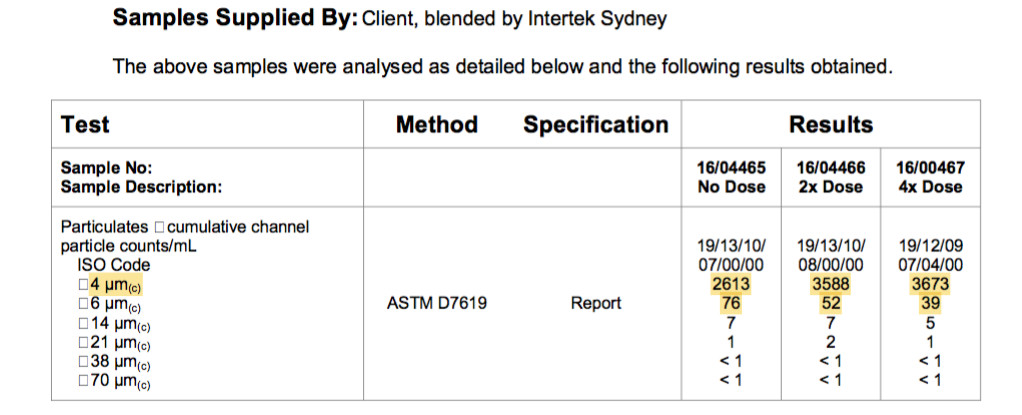
This is a fuel sample from an Australian major retail supplier. The fuel is an automotive grade diesel that meets Australian Fuel Standards with a sulphur limit of 10ppm.
Each particle is a hydrocarbon chain and is counted as one and if there are multiple agglomerations of hydrocarbon chains they are also counted as one.
The particle count under 4 microns of 2613 on the left column and when the fuel is treated with the dispersant, the particle count increases by 30% to 3588. Identifying a number of existing chain agglomerations.
The larger 6 micron and 14 microns particles are also broken down, again identifying larger agglomerations in the fuel.
This “before and after” ASTM D7619 ISO particle count has identified a number of agglomerations in the fuel and by separating all the agglomerated and unstable double bonded hydrocarbons, the dispersant has repaired the fuel to its intended composition.
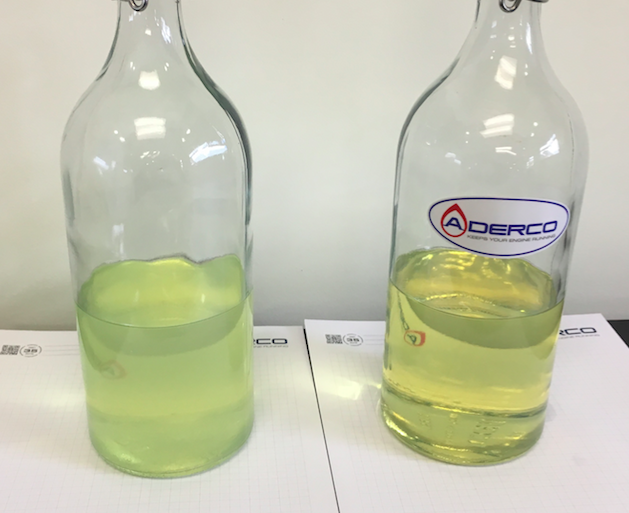
Above image, the fuel is from the same source. On the left un-treated and on the right treated. The cloudiness of the un-treated fuel on the left is visual evidence of agglomerations and emulsified water droplets from condensations. On the right the fuel is clear without agglomerations and we can see the small amount of water droplets being separated on the video below.
Why does fuel perform better when a dispersant has reversed the agglomerations?
Once fuel has been conditioned and the agglomerations have dispersed. It becomes finer as it had been intended to be in the first place.
When sprayed out of the injectors, the droplets have now increased in numbers by about 30% and the droplets are also about 30% smaller.
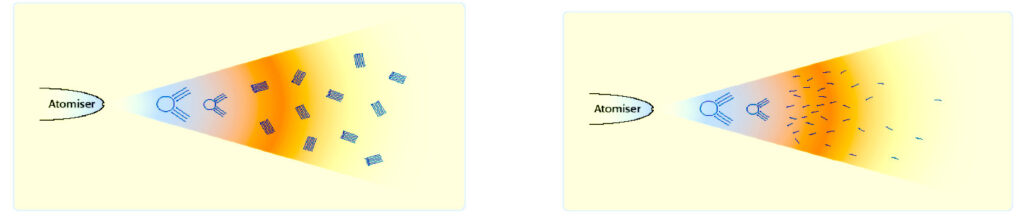
With a more even spray and all the hydrocarbon particles individual and of equal size. The droplets are now smaller and more in number. More air can reach the droplets surface area and less pressure and heat is required for a complete combustion.
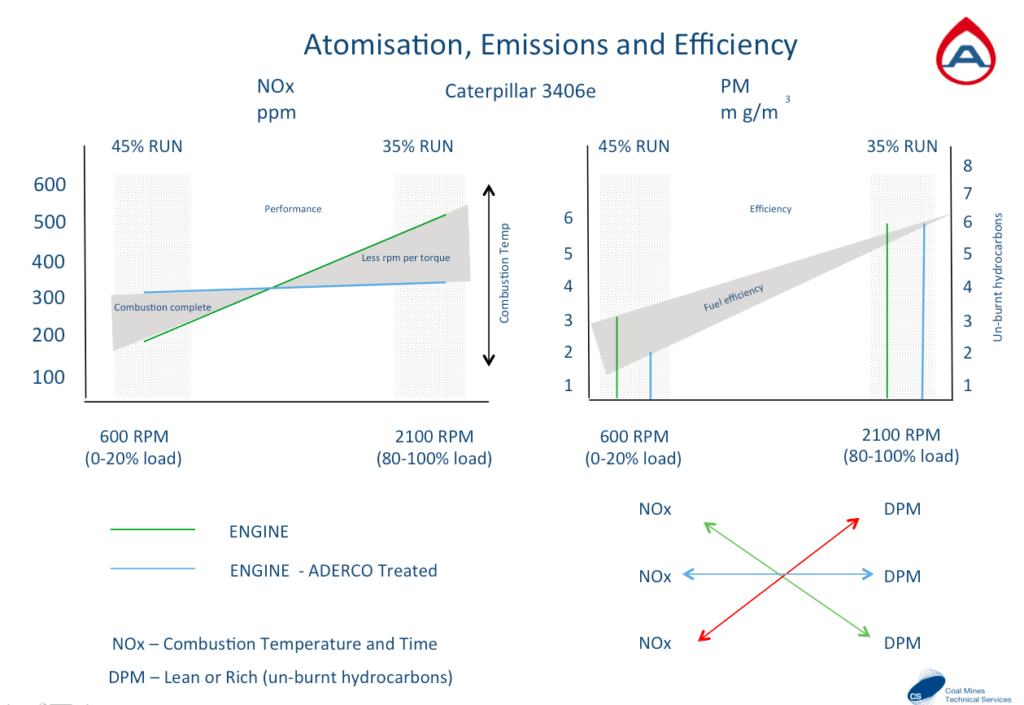
NOx is directly linked to combustion heat (more heat = more NOx)
PM Particulate Matter is most often unburnt fuel (less PM = more fuel efficiency)
This engine has been tested for emissions on two occasions with the same fuel. Once before the fuel was treated and then once after the fuel was treated. The combustion at idle improves considerably with treated fuel (blue line) with a higher heat achieved and less Particulate Matter (unburnt fuel) can be seen on the right. The same applies when at full load the treated fuel burns as much fuel without having to reach as high a temperature. The fuel performs as it should when conditioned.
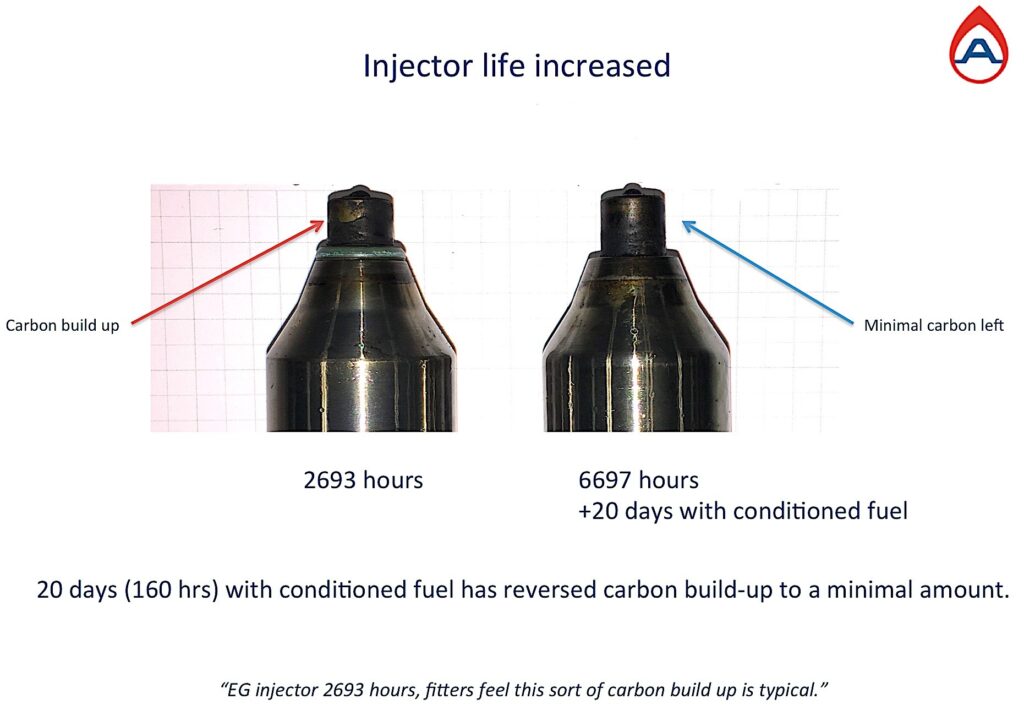
Both injectors are from identical engines, using the same fuel and running the same operations.
The injector on the left has only 2,693 hours and the carbon shell has been cracked to show the thickness of carbon has built over time by a recurring incomplete combustion.
The injector on the right has 6,697 hours and hardly any carbon. Within 160 hours of a recurring complete combustion due to conditioned fuel, the carbon is no longer there or able to build.
Carbon and soot are the by-products of unburnt hydrocarbons and logically agglomerated particles are larger and therefore harder to burn. By dispersing them we can achieve a complete combustion and carbon and soot cannot re-form or reoccur.
The fix
Though as we have discussed refinery evolution has gradually made fuel less stable, it has not gone unnoticed by major fuel suppliers. MTBE, Methyl tertiary butyl ethers, is a widely used method to oxygenate fuel, but now slowly being banned by the EPA in many states in the US. These products also have dosage risks.
The solution
Most recently BP and Exxon Mobil have announced and advertised premium fuels with detergent-based additives. An acknowledgment that treatment and prevention at the source is a better method of reaching a complete combustion, rather than enhancing fuel to amplify a bigger bang.
Repairing and protecting fuel is the only sustainable method of preventing fuel related operational issues. All OPEX benefits of fuel efficiency, component optimisation and extending performance between service schedules are simply the consequential effects of the detergent additive repairing and preventing instabilities in fuel. There are no shortcuts.
Conclusion
In this paper I’ve focused on combustion, there are a number of different additives for different purposes, there are solvents, some that are solvent and detergent blends and there are some that are 100% vegetal and sustainable and can deliver multiple consequential benefits.
I hope my explanation gives an understanding of how to identify types and why it is important to use the right additives in fuel today.
Flash points – are a good indicator.
Finally
Fuel, oil refining, hydrocarbons, and additives are a complex subject. This paper is only intended as an introduction by scraping the surface in 1500 words or 10 minutes of reading.
Please feel free to contact me to discuss further.
[email protected] – Aderco Sustainable Fuel Treatment
Supporting documents available on request for clients and qualified prospective clients;
- Sydney Ferries Trial – 2015/2016
- Coal Technical Mines Services – Emission Certificates
- INTERTEK LAB ASTM D7619 – Particle Agglomeration
- Chevron diesel-fuel-tech-review. highlights.pdf P.84-87
- TAFE SWSI – Dyno test 2015